Industrial Water Tanks Dealers in Bangalore
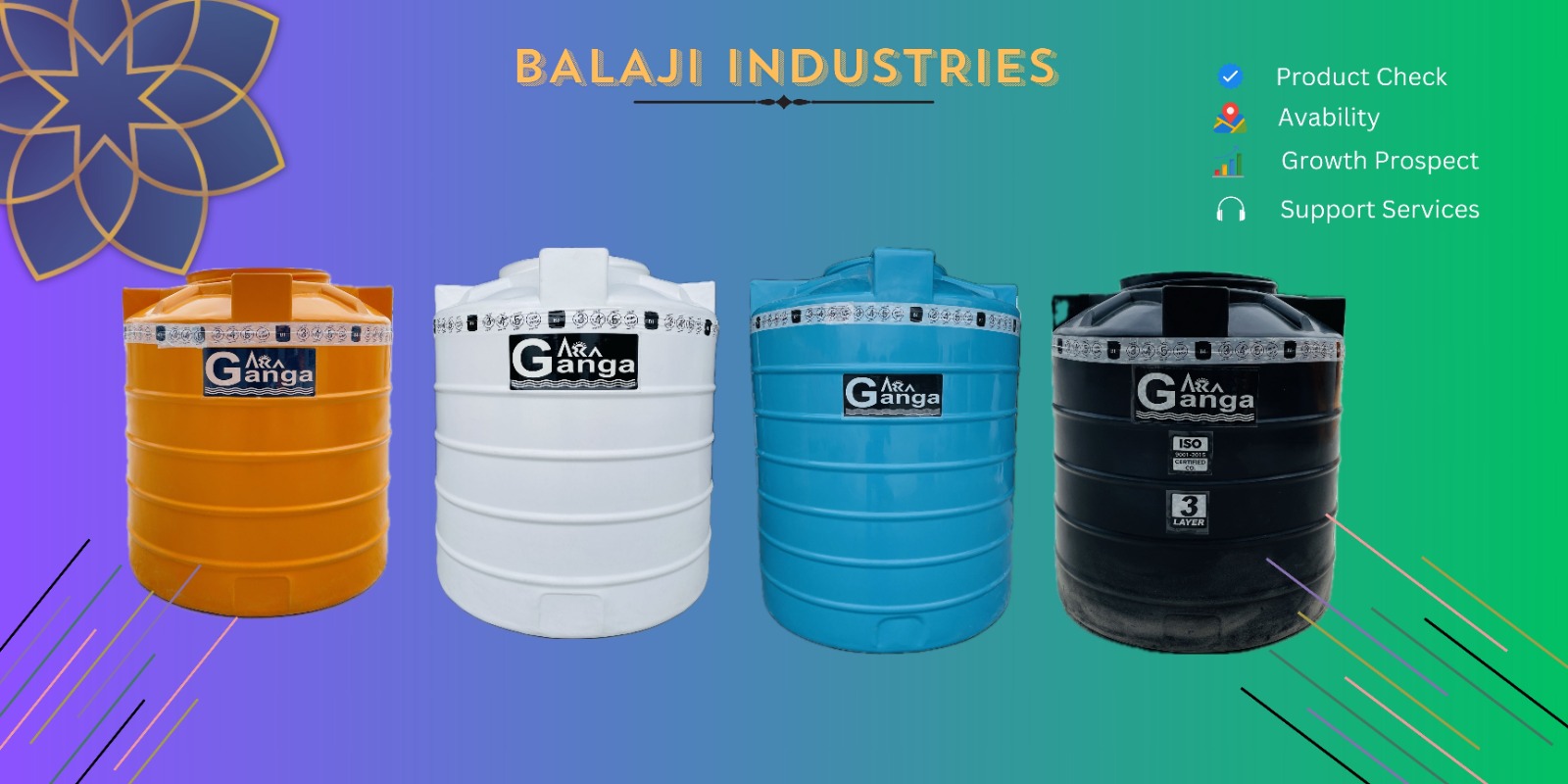
Contact : +919036763585
Industrial water tanks are essential storage solutions used across various sectors such as manufacturing, agriculture, construction, and public utilities. These tanks play a critical role in water storage for industrial processes, firefighting, wastewater management, and even potable water storage. They are typically larger, more robust, and specially designed to meet the demanding requirements of industrial use compared to standard residential tanks.
Types of Industrial Water Tanks
Industrial water tanks come in various materials, each offering distinct advantages depending on the application. Some of the most common types include:
-
Steel Water Tanks: Known for their durability and strength, steel tanks (both stainless and carbon steel) are used in industries that require high-capacity water storage. Stainless steel tanks are particularly beneficial in industries where hygiene and corrosion resistance are priorities, such as in food and beverage processing.
-
Fiberglass Water Tanks: These tanks are highly resistant to corrosion, making them ideal for storing both potable and non-potable water. Fiberglass tanks are lightweight compared to steel and have high structural integrity, making them suitable for chemical plants, refineries, and water treatment facilities.
-
Polyethylene (Plastic) Water Tanks: Made from high-density polyethylene (HDPE), these tanks are cost-effective and resistant to many chemicals, making them suitable for industrial uses where moderate durability and chemical resistance are sufficient. They are also lightweight, easy to install, and often used in agriculture, irrigation, and wastewater storage.
-
Concrete Water Tanks: These tanks are long-lasting and capable of holding large volumes of water, often used in large-scale industrial applications such as irrigation projects or public utilities. They are highly durable, but installation is more labor-intensive and costly compared to other types.
-
Bladder Tanks: These are collapsible tanks typically made from flexible, heavy-duty fabrics. They are easy to transport and deploy, making them useful for temporary water storage needs, emergency response situations, or mobile industrial operations.
Key Applications
-
Manufacturing: Water is an integral part of many manufacturing processes, such as cooling, cleaning, and chemical production. Industrial water tanks in these settings often store both potable water and process water, and must be equipped to handle large volumes and various conditions.
-
Agriculture and Irrigation: Farmers and agricultural businesses use industrial tanks to store water for irrigation, livestock, and crop production. These tanks help ensure that water is available during dry periods and support efficient farm management.
-
Fire Suppression: Many industrial facilities have on-site water tanks dedicated to firefighting purposes. These tanks are required by safety regulations to hold a minimum amount of water for emergency use, helping to protect property and personnel in case of a fire.
-
Wastewater Management: Industrial wastewater must be properly treated and stored to prevent environmental contamination. Industrial water tanks used in wastewater management are designed to store both treated and untreated wastewater until it can be properly disposed of or recycled.
-
Potable Water Storage: Certain industries, such as food processing and pharmaceuticals, require access to high-quality water. Tanks used for potable water storage in these industries must adhere to stringent hygiene and safety regulations to ensure water quality.
Factors to Consider When Choosing an Industrial Water Tank
When selecting an industrial water tank, several key factors must be considered:
-
Capacity: Industrial water tanks can range from a few hundred gallons to millions of gallons. The tank’s capacity should align with the volume of water required for the specific industrial operation.
-
Material: The material used to construct the tank is crucial, as it impacts the tank’s durability, chemical resistance, and maintenance requirements. Stainless steel is ideal for harsh environments, while polyethylene is often chosen for less demanding applications.
-
Location: The placement of the tank, whether above ground or underground, also affects its design and material requirements. Underground tanks may need more robust construction to withstand external pressures.
-
Environmental Conditions: Factors such as temperature, exposure to chemicals, and UV radiation will influence the choice of tank material and design.
-
Regulatory Compliance: Depending on the industry, there may be local or international standards that govern water storage systems. Ensuring compliance with these regulations is essential to avoid penalties and ensure safe operation.
Conclusion
Industrial water tanks are indispensable assets across various industries, providing essential water storage solutions that support critical operations, from manufacturing to agriculture and firefighting. With a variety of materials, sizes, and configurations available, choosing the right industrial tank requires a careful assessment of the specific application, environmental conditions, and regulatory requirements. Proper selection and maintenance of industrial water tanks ensure operational efficiency, safety, and sustainability for industrial facilities.