Storage Tank Manufacturers in Bangalore
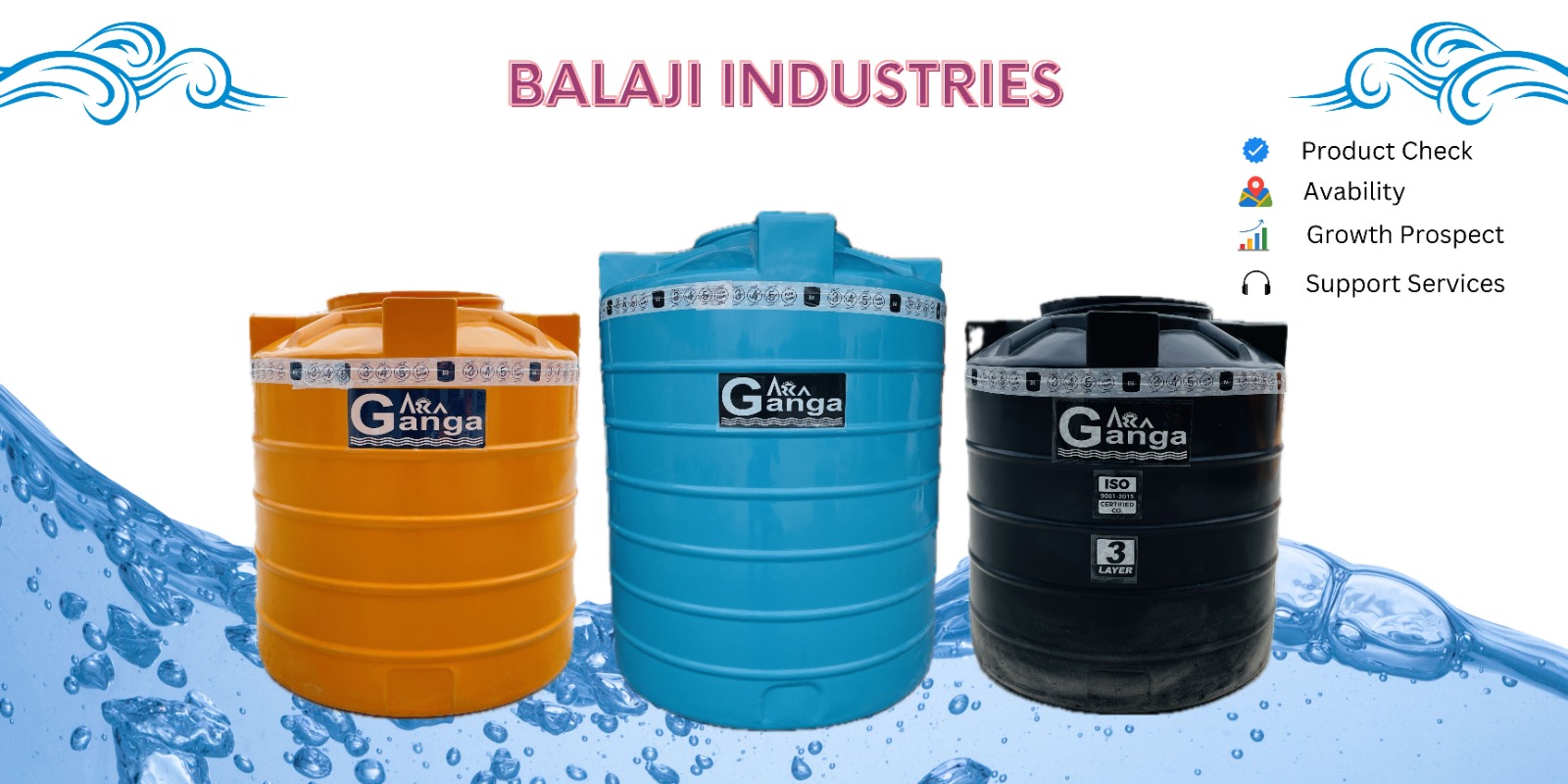
Contact : +919036763585
Storage tanks are essential components in various industries, including chemical, oil and gas, water treatment, and agriculture. They are designed to hold liquids, gases, or solids and are crucial for managing and storing different types of materials. The manufacturing of storage tanks involves several stages, including design, material selection, fabrication, and testing. This overview will cover the key aspects of storage tank manufacturing, emphasizing the processes, materials, and considerations involved in producing high-quality and reliable tanks.
Design and Engineering
The design of storage tanks begins with understanding the specific requirements of the application. This includes the type of material to be stored, the volume of storage required, environmental conditions, and safety regulations. Engineers and designers use this information to create detailed specifications and drawings.
-
Type of Tank: Different types of storage tanks are used for various applications, such as vertical or horizontal tanks, cylindrical or spherical shapes, and above-ground or underground installations. The choice of tank type depends on factors like space constraints, volume requirements, and environmental considerations.
-
Material Selection: The choice of material is crucial for ensuring the durability and safety of the tank. Common materials include carbon steel, stainless steel, fiberglass, and reinforced concrete. Each material has its advantages and is selected based on factors such as corrosion resistance, strength, and cost.
-
Design Standards: Storage tank designs must adhere to industry standards and regulations to ensure safety and reliability. Standards such as those from the American Petroleum Institute (API), American Society of Mechanical Engineers (ASME), and other international standards provide guidelines for design, construction, and testing.
Fabrication Process
Once the design is finalized, the fabrication process begins. This involves several key steps:
-
Material Preparation: The selected materials are cut, shaped, and prepared for assembly. For metal tanks, this involves cutting sheets or plates and forming them into the required shapes. For fiberglass tanks, it involves preparing the resin and fiber materials.
-
Welding and Assembly: For metal tanks, the sheets or plates are welded together to form the tank. This process requires precision to ensure strong and leak-proof joints. Welding techniques such as arc welding, MIG welding, or TIG welding may be used, depending on the material and design requirements.
-
Reinforcement: Depending on the tank design and material, additional reinforcement may be required. This can include adding internal supports, bracing, or reinforcement ribs to enhance the tank’s strength and stability.
-
Surface Treatment: After assembly, the tank undergoes surface treatment to protect against corrosion and ensure longevity. This may involve applying protective coatings, paint, or linings, depending on the material and the stored substance.
Testing and Quality Assurance
Quality assurance is a critical aspect of storage tank manufacturing. Various tests are conducted to ensure that the tank meets design specifications and safety standards:
-
Hydrostatic Testing: The tank is filled with water or another liquid to test for leaks and structural integrity. This test helps identify any weak spots or potential issues before the tank is put into service.
-
Pressure Testing: For tanks designed to hold gases or liquids under pressure, pressure testing is conducted to ensure the tank can handle the specified pressure levels without failure.
-
Inspection and Certification: Tanks are inspected by qualified personnel to ensure compliance with design standards and safety regulations. Certification from relevant authorities may be required, depending on the application and industry.
-
Documentation: Detailed records of the manufacturing process, including design specifications, materials used, and test results, are maintained for quality assurance and regulatory compliance.
Installation and Maintenance
Once the tank has passed all tests and inspections, it is ready for installation. The installation process involves:
-
Site Preparation: The installation site must be prepared to support the tank's weight and ensure proper alignment. This may involve constructing a foundation or platform and ensuring adequate drainage.
-
Transportation and Assembly: The tank is transported to the installation site and assembled if necessary. For large tanks, this may involve specialized equipment and techniques to ensure proper placement and alignment.
-
Connection and Commissioning: The tank is connected to the relevant piping and support systems. Commissioning involves testing the tank in its installed position to ensure it operates correctly and meets all performance requirements.
-
Ongoing Maintenance: Regular maintenance is essential to ensure the tank’s longevity and safe operation. This includes inspecting for signs of wear or corrosion, performing necessary repairs, and ensuring that the tank remains in compliance with safety standards.
Conclusion
Storage tank manufacturing is a complex process that requires careful planning, precise fabrication, and rigorous testing to ensure safety and reliability. From the initial design and material selection to fabrication, testing, and installation, each stage plays a crucial role in producing a high-quality storage tank. Adhering to industry standards and regulations, as well as implementing effective quality assurance practices, is essential for ensuring that storage tanks meet the demands of their intended applications and provide reliable service over their operational life.