Water Storage Tank Manufacturers in India
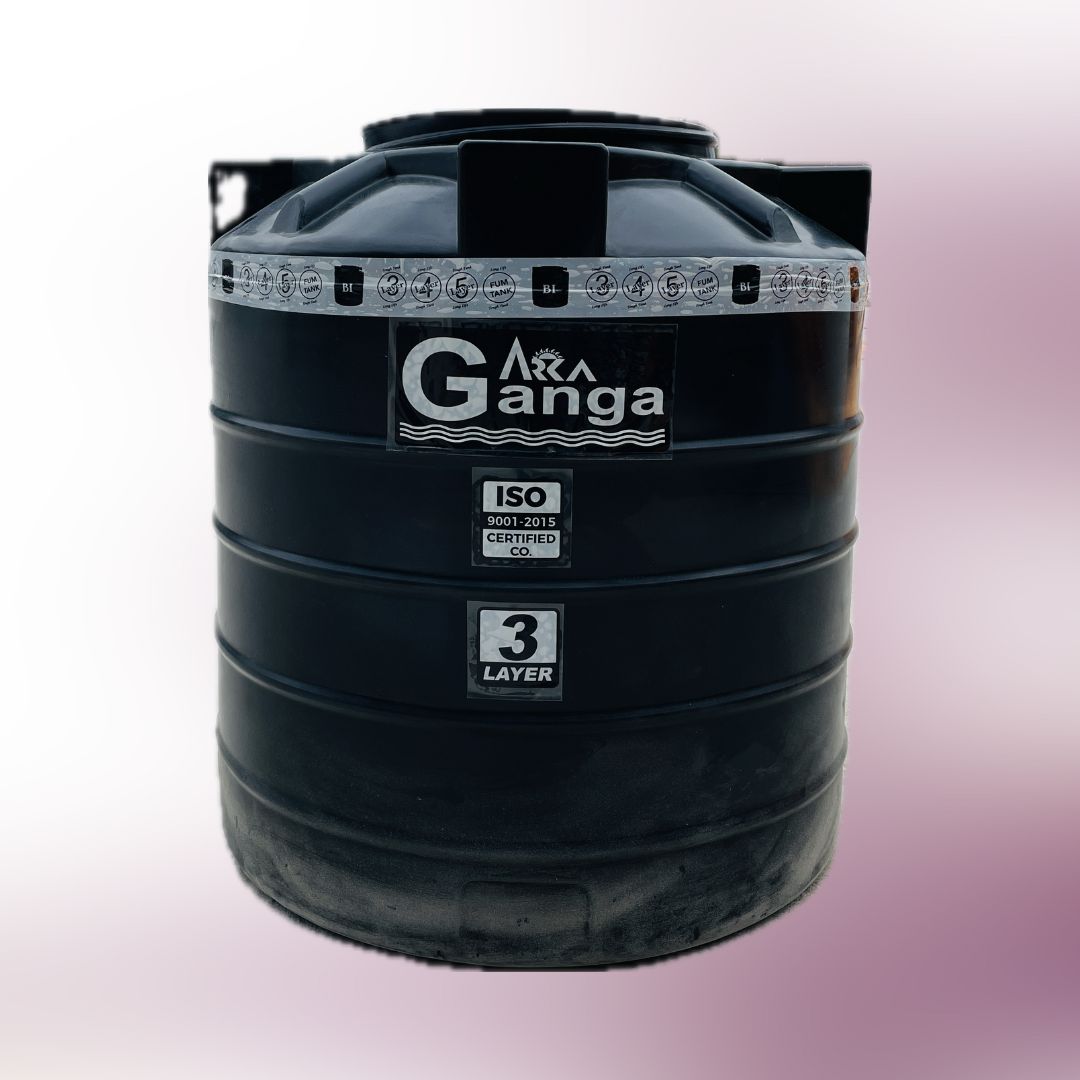
Contact : +919036763585
Water Tank Manufacturers in India
Water tanks are essential infrastructure components, serving crucial roles in storing and supplying water for residential, commercial, and industrial use. The manufacture of water tanks involves a complex process, combining engineering expertise with material science to produce durable and efficient storage solutions. Here’s a comprehensive overview of the water tank manufacturing process.
1. Types of Water Tanks
Before delving into manufacturing, it’s important to understand the different types of water tanks available:
- Plastic Tanks: Often made from polyethylene or polypropylene, plastic tanks are popular due to their resistance to corrosion, lightweight nature, and ease of installation. They are ideal for residential and small-scale commercial uses.
- Concrete Tanks: These tanks are robust and suited for large-scale applications, including municipal water storage. They are made from reinforced concrete and can be either above-ground or underground.
- Steel Tanks: Steel tanks are favored for their strength and durability. They are often used in industrial and large commercial settings. Steel tanks can be coated or lined to prevent corrosion.
- Fiberglass Tanks: Lightweight and resistant to chemicals, fiberglass tanks are used in both residential and industrial applications. They are strong and less susceptible to environmental factors.
2. Manufacturing Process
1. Design and Engineering:
The manufacturing process starts with design and engineering. Engineers and designers assess the requirements, including the tank’s size, capacity, material, and intended use. Advanced computer-aided design (CAD) software is used to create precise designs, ensuring structural integrity and functionality.
2. Material Selection:
Choosing the right material is crucial for the tank's durability and performance. For plastic tanks, high-density polyethylene (HDPE) or polypropylene is selected for its durability and resistance to UV rays and chemicals. Concrete tanks use a mixture of cement, sand, gravel, and water, often reinforced with steel rebar. Steel tanks are made from galvanized steel or stainless steel to resist corrosion. Fiberglass tanks use a blend of glass fibers and resin.
3. Fabrication:
-
Plastic Tanks: The fabrication process typically involves blow molding or rotational molding. In blow molding, plastic pellets are melted and injected into a mold to form the tank. Rotational molding involves rotating a mold filled with plastic resin, allowing the material to coat the interior evenly.
-
Concrete Tanks: The fabrication involves pouring a concrete mixture into molds. Reinforcing steel bars are placed in the molds to strengthen the concrete. Once the concrete cures, the mold is removed, and the tank is inspected for any defects.
-
Steel Tanks: Steel sheets are cut, shaped, and welded or bolted together to form the tank. The interior is coated or lined to prevent corrosion. For large tanks, sections are often pre-fabricated and assembled on-site.
-
Fiberglass Tanks: Fiberglass tanks are manufactured using a process called filament winding or hand lay-up. Fiberglass strands are wound onto a rotating mandrel or layered by hand and then coated with resin. The tank is cured to harden the material.
4. Quality Control:
Quality control is a critical step in tank manufacturing. Tanks undergo rigorous testing to ensure they meet safety and performance standards. This includes pressure tests, leak tests, and inspections for structural integrity and material defects.
5. Installation and Maintenance:
Once manufactured, tanks are either delivered as complete units or in parts for assembly on-site. Proper installation is crucial for ensuring the tank's longevity and efficiency. Regular maintenance, including inspections and cleaning, is necessary to prevent issues such as leaks, corrosion, and sediment buildup.