Water Tank Manufacturers in Karnataka
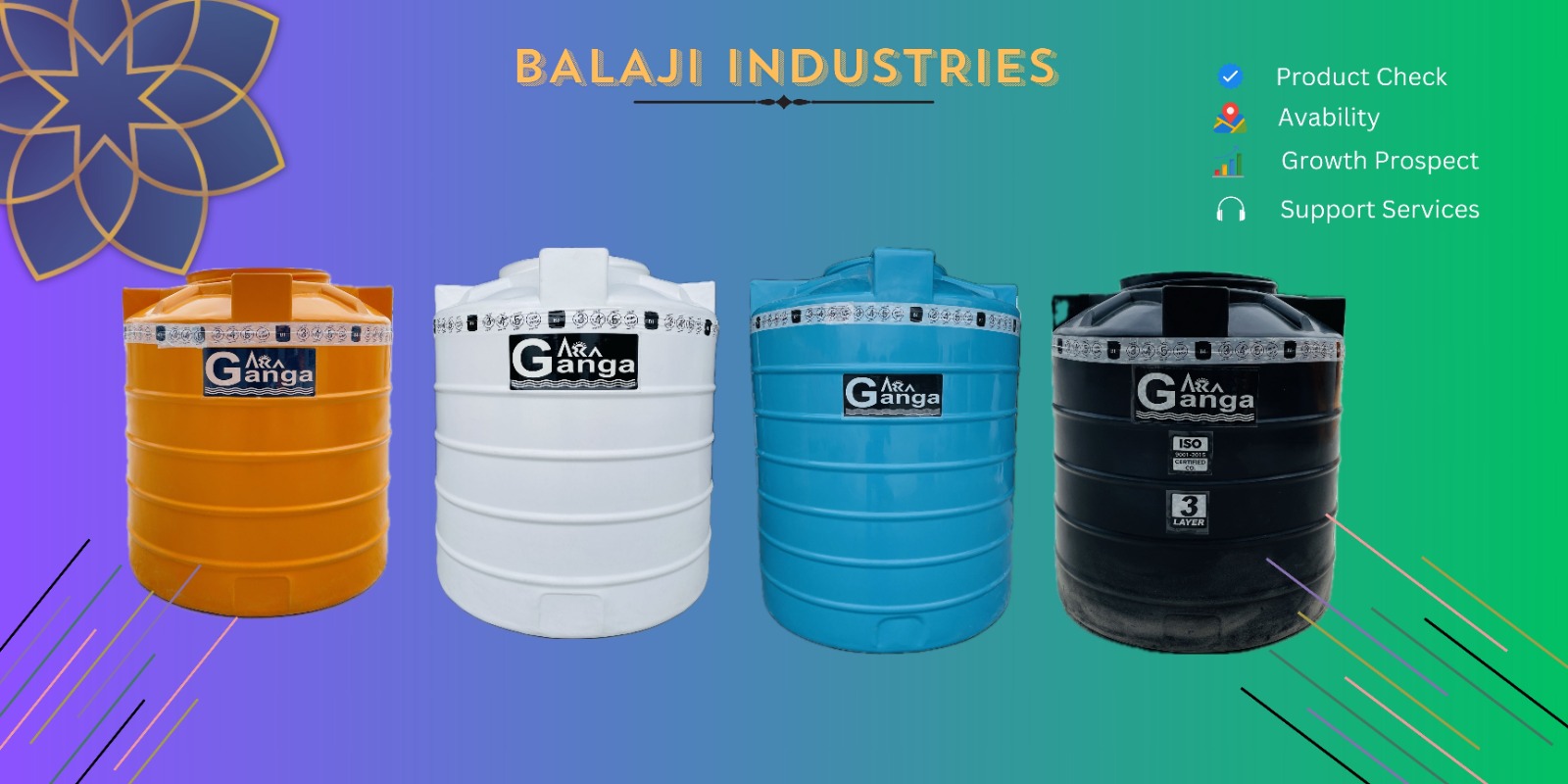
Contact : +919036763585
Water tank manufacturing is a vital industry that produces containers designed to store water safely and efficiently for various applications, including residential, agricultural, industrial, and municipal needs. The process involves using different materials, each chosen based on durability, environmental impact, cost, and intended use. Water tanks come in various shapes and sizes and are manufactured using materials such as plastic (polyethylene or polypropylene), concrete, fiberglass, and steel.
1. Materials and Their Advantages
-
Plastic (Polyethylene/Polypropylene): One of the most common materials in water tank manufacturing, plastic is popular because it is lightweight, resistant to corrosion, and can be molded into various shapes and sizes. Plastic tanks are often used for residential and agricultural applications due to their affordability and versatility. The manufacturing process for plastic tanks involves rotational molding, where powdered plastic is placed in a mold and heated while being rotated to form a uniform thickness.
-
Steel: Steel tanks are typically used for industrial applications where high-strength materials are required. These tanks are durable and capable of withstanding high pressure, making them suitable for large storage capacities and use in challenging environments. Galvanized steel and stainless steel are popular choices for their rust-resistant properties, although maintenance may be needed to prevent corrosion.
-
Concrete: Concrete tanks are widely used in municipal and large-scale applications due to their structural strength and durability. These tanks are cast on-site or pre-cast and transported, offering long-term storage solutions, especially for underground installations. They are more resistant to temperature changes but can be costly and require significant labor for installation.
-
Fiberglass: Fiberglass tanks are corrosion-resistant, lightweight, and durable. They’re often used in areas where high-strength tanks are needed, and they can also resist various chemical exposures, making them suitable for industrial and agricultural applications.
2. Manufacturing Process
The manufacturing of water tanks involves several steps, each critical for ensuring the tank’s structural integrity, safety, and functionality.
-
Design and Prototyping: The process begins with designing the tank based on its intended purpose and the customer’s specifications. Engineers create 3D models to optimize shape, capacity, and structure, keeping in mind factors like ease of installation, storage capacity, and environmental considerations.
-
Material Preparation and Molding: For plastic tanks, rotational molding is the preferred method, while steel tanks are manufactured through welding and fabrication. Concrete tanks may be cast on-site or at a manufacturing facility, depending on their size and design requirements. Fiberglass tanks are manufactured by layering fiberglass sheets with resin, then curing the structure to ensure strength.
-
Assembly and Quality Control: Each tank undergoes rigorous quality checks to ensure durability, leak-proofing, and compliance with industry standards. Tanks may be coated with UV-resistant or anti-corrosion layers, especially for materials like steel and plastic, to enhance longevity.
3. Types of Water Tanks
Water tanks vary based on design and function:
- Above-Ground Tanks: These are typically used in residential and agricultural settings for ease of installation and accessibility.
- Underground Tanks: Ideal for saving space and maintaining a low visual profile, underground tanks are more common in urban areas and can help maintain cooler water temperatures.
- Modular Tanks: These are versatile, allowing for expansion as storage needs grow, and are often made of interlocking steel or fiberglass panels.
4. Sustainability and Innovation
Modern water tank manufacturing emphasizes sustainability. Eco-friendly materials, improved insulation, and UV-protective coatings help increase tank longevity and reduce environmental impact. Additionally, innovations in smart water tanks with sensors and IoT capabilities allow real-time monitoring of water levels, quality, and tank maintenance needs.
5. Quality Standards and Certifications
Water tanks must adhere to safety and health standards, particularly for potable water storage. Standards vary by region, but manufacturers often follow ISO 9001 for quality management systems and NSF/ANSI standards for drinking water safety. Testing protocols, such as hydrostatic testing for leak-proofing and strength testing for durability, ensure that the tanks meet these requirements.
6. Challenges and Future Prospects
The industry faces challenges like fluctuating raw material costs, environmental concerns, and the need for skilled labor. However, innovations in material science, such as the use of recycled plastics or bio-based materials, offer promising solutions. Additionally, as climate change drives the need for water conservation, the demand for efficient storage solutions is expected to grow.
In summary, water tank manufacturing is a complex industry focused on creating durable, safe, and environmentally conscious solutions for water storage. By balancing material science, manufacturing techniques, and quality control, manufacturers are meeting the increasing demand for reliable water storage options across sectors.