Water Tank Manufacturers Near Me
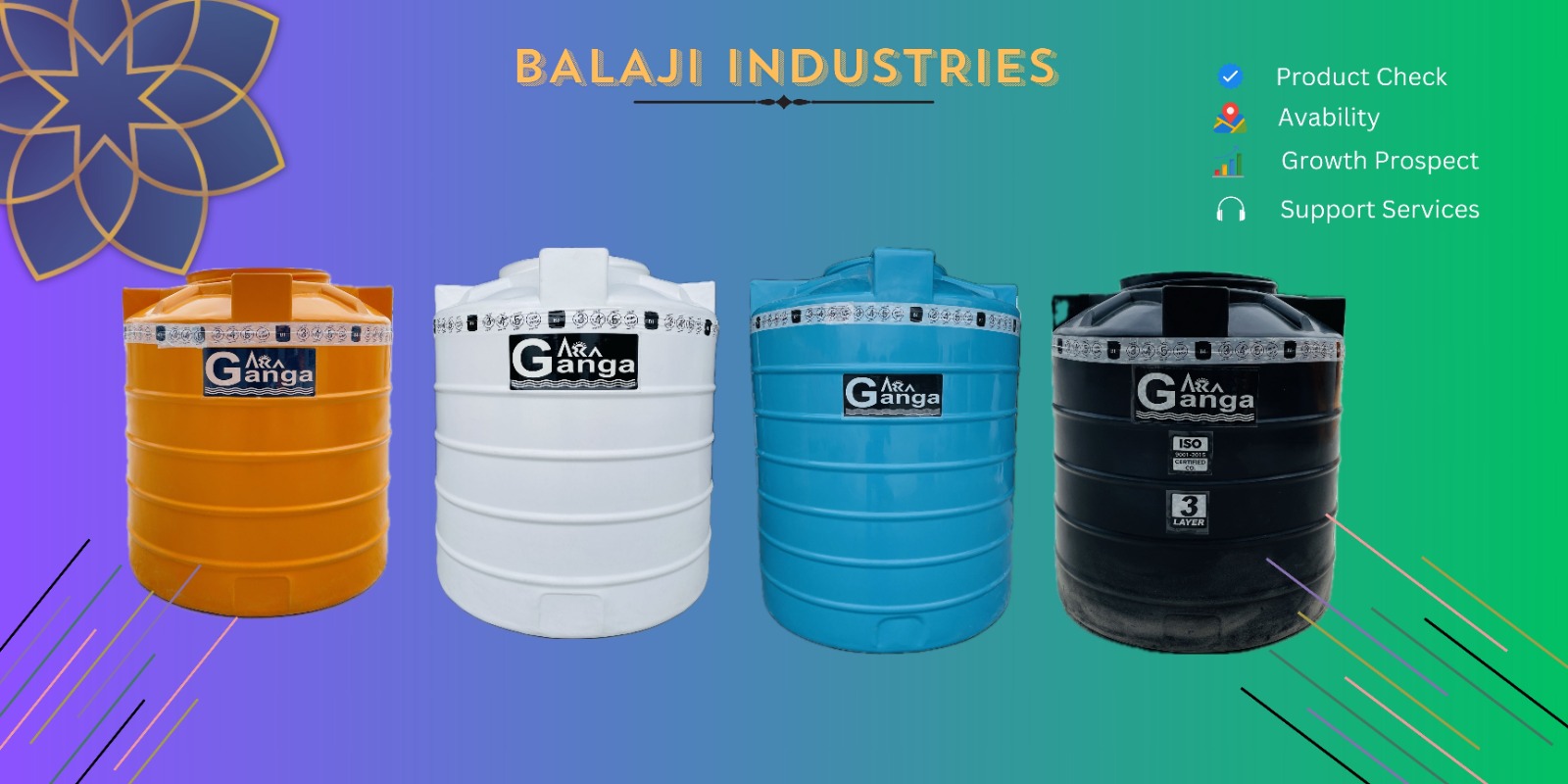
Water Tank Manufacturing
Water tanks play a crucial role in the storage and management of water for residential, commercial, and industrial purposes. They are essential for ensuring a consistent supply of water, whether for drinking, irrigation, or industrial processes. The manufacturing of water tanks involves a blend of engineering, material science, and production techniques, and it varies depending on the type of tank being produced. This overview will cover the key aspects of water tank manufacturing, including types, materials, processes, and quality considerations.
Types of Water Tanks
Water tanks come in various types, each designed to meet specific needs and applications. The primary types include:
-
Concrete Tanks: Often used for large-scale storage, concrete tanks are durable and capable of handling significant volumes of water. They are commonly found in municipal and industrial settings.
-
Steel Tanks: Steel tanks are robust and can be customized to different sizes. They are used in both large and small-scale applications. Stainless steel is particularly popular for its resistance to corrosion.
-
Plastic Tanks: Made from materials such as polyethylene, plastic tanks are lightweight and resistant to corrosion. They are commonly used in residential settings and are often available in various sizes and shapes.
-
Fiberglass Tanks: These tanks are known for their strength and resistance to corrosion. Fiberglass tanks are used in both residential and industrial applications and are often chosen for their durability and longevity.
-
Bladder Tanks: Designed to be flexible and collapsible, bladder tanks are used in temporary storage situations. They are typically used in emergency situations or for temporary water storage.
Materials Used in Water Tank Manufacturing
The choice of material for a water tank significantly affects its performance, durability, and cost. Here’s a closer look at the materials commonly used:
-
Concrete: Concrete tanks are reinforced with steel rebar and are known for their strength and longevity. They are often used for large-scale storage due to their ability to handle heavy loads and resist environmental factors.
-
Steel: Steel tanks are either carbon steel or stainless steel. Carbon steel tanks are coated to prevent rust, while stainless steel tanks are more resistant to corrosion and are used in environments where rust is a concern.
-
Plastic: Polyethylene is the most common plastic used in water tank manufacturing. It is lightweight, resistant to corrosion, and relatively inexpensive. High-density polyethylene (HDPE) is often used for its strength and durability.
-
Fiberglass: Fiberglass tanks are made from a combination of glass fibers and resin. This material provides high strength and resistance to various chemicals, making it suitable for both industrial and residential use.
Manufacturing Processes
The manufacturing process for water tanks varies depending on the material used. Here’s a general overview of the processes for different types of tanks:
-
Concrete Tanks: The manufacturing process for concrete tanks involves creating molds, pouring concrete into these molds, and allowing the concrete to cure. Reinforcement bars are added to enhance the strength of the tank. Once cured, the tank is removed from the mold and undergoes quality checks.
-
Steel Tanks: For steel tanks, the process involves cutting and shaping steel sheets, welding them together, and applying coatings to prevent rust. The tanks are then tested for leaks and structural integrity before being sent for final finishing.
-
Plastic Tanks: Plastic tanks are typically manufactured using rotational molding or blow molding processes. In rotational molding, plastic is melted and rotated inside a mold to form the tank. Blow molding involves blowing air into a molten plastic tube to shape it into a tank.
-
Fiberglass Tanks: The manufacturing process for fiberglass tanks involves layering glass fibers and resin inside a mold. The layers are allowed to cure, and the finished tank is removed from the mold. The tank is then inspected for any defects.
Quality Considerations
Quality control is essential in water tank manufacturing to ensure the tanks meet safety and performance standards. Key quality considerations include:
-
Material Quality: The raw materials used in manufacturing must meet specific standards to ensure the tank’s durability and safety. For example, plastics must be UV-resistant, and steel must be properly coated to prevent rust.
-
Structural Integrity: Tanks must be tested for structural integrity to ensure they can handle the intended load. This includes checking for leaks, cracks, and overall strength.
-
Compliance with Standards: Water tanks must comply with relevant industry standards and regulations, such as those set by the American Water Works Association (AWWA) or other local standards.
-
Inspection and Testing: Regular inspections and testing throughout the manufacturing process help identify and address any issues before the tanks are delivered to customers. This includes pressure testing, visual inspections, and other quality assurance measures.
Conclusion
The manufacturing of water tanks is a complex process that requires careful consideration of materials, processes, and quality control. Each type of tank—whether concrete, steel, plastic, or fiberglass—has its unique advantages and applications. By adhering to stringent quality standards and employing advanced manufacturing techniques, manufacturers ensure that water tanks meet the needs of various applications while providing reliable and durable water storage solutions.