Water tank manufacturers Near Me
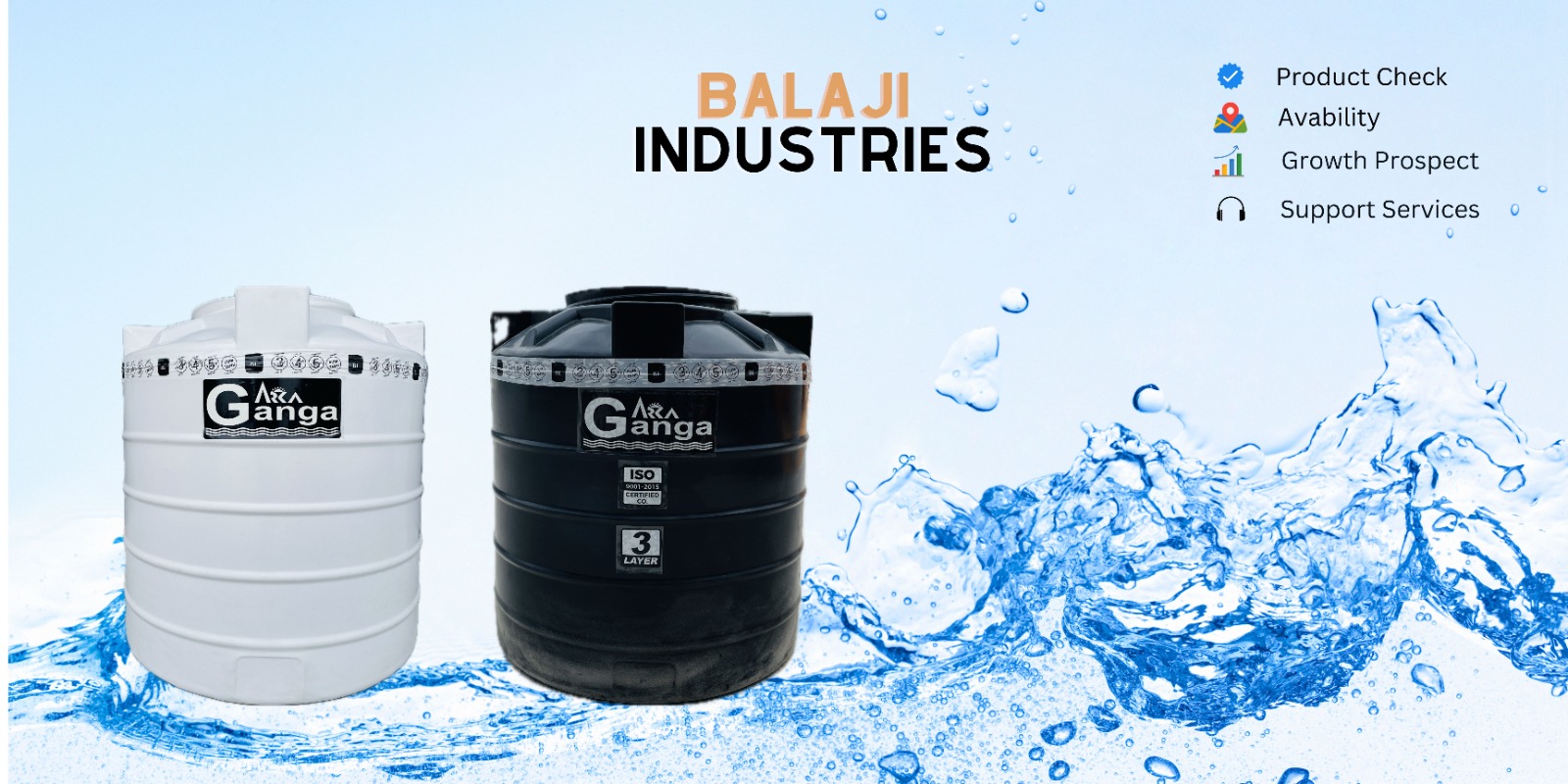
Contact : +919036763585
Water Tank Manufacture: An Overview
Introduction
Water tanks play a crucial role in water storage and management across various sectors, including residential, commercial, and industrial applications. Manufacturing water tanks involves a complex process that ensures the production of durable, reliable, and efficient storage solutions. This article provides an overview of the water tank manufacturing process, highlighting the materials used, manufacturing techniques, and key considerations for producing high-quality tanks.
Materials Used
The choice of material for water tank manufacturing is pivotal to the tank's performance, longevity, and safety. Common materials include:
-
Polyethylene (Plastic): Polyethylene tanks are popular due to their lightweight nature, resistance to corrosion, and ease of installation. They are manufactured using rotational molding, which ensures uniform wall thickness and durability. Plastic tanks are suitable for residential and small-scale applications.
-
Fiberglass: Fiberglass tanks are known for their strength, resistance to chemical corrosion, and long lifespan. They are manufactured using a process called filament winding, where glass fibers are wrapped around a mold and impregnated with resin. These tanks are often used in industrial applications where chemical resistance is essential.
-
Steel: Steel tanks, including those made from carbon steel or stainless steel, offer high strength and durability. They are often used for large-scale storage needs. Steel tanks are manufactured through welding and bolting processes, with coatings applied to prevent rust and corrosion.
-
Concrete: Concrete water tanks are known for their robustness and are commonly used in large-scale water storage applications. They are typically cast in place or pre-cast and assembled on-site. Concrete tanks are reinforced with steel rebar to enhance their structural integrity.
Manufacturing Techniques
The manufacturing process for water tanks varies depending on the material used. Here’s a brief overview of common techniques:
-
Rotational Molding (for Plastic Tanks): In this process, plastic powder is placed into a hollow mold, which is then heated and rotated around two perpendicular axes. The plastic melts and coats the inside of the mold, forming a seamless, uniform tank. Once cooled, the mold is opened, and the tank is removed.
-
Filament Winding (for Fiberglass Tanks): This technique involves winding glass fibers impregnated with resin around a rotating mold. The fibers are applied in a specific pattern to enhance the tank's strength and durability. After winding, the tank is cured to harden the resin.
-
Welding and Bolting (for Steel Tanks): Steel tanks are constructed by welding steel plates together to form the tank structure. Bolted steel tanks are assembled from pre-fabricated panels that are bolted together. After assembly, the tank is coated with anti-corrosive paint or linings.
-
Casting (for Concrete Tanks): Concrete tanks are either cast in place using formwork or pre-cast in a factory setting. In both methods, concrete is poured into molds and allowed to cure. Reinforcement with steel rebar is done to provide additional strength.
Key Considerations
When manufacturing water tanks, several factors must be considered to ensure the final product meets safety and performance standards:
-
Capacity and Size: Tanks must be designed to meet specific capacity requirements, whether for small residential use or large industrial applications. Proper sizing ensures that the tank meets the demand for water storage.
-
Durability and Maintenance: The choice of material and manufacturing process affects the tank's durability and maintenance needs. For instance, plastic and fiberglass tanks generally require less maintenance compared to steel tanks, which may need regular inspection for rust.
-
Regulatory Compliance: Water tanks must comply with local regulations and standards, particularly those related to health and safety. This includes ensuring that the materials used are safe for potable water storage.
-
Installation and Handling: The design should facilitate easy installation and handling. Tanks should be designed to withstand environmental conditions and loads during transportation and installation.
Conclusion
The manufacture of water tanks is a multifaceted process that requires careful selection of materials, precise manufacturing techniques, and consideration of various factors to ensure the production of reliable and efficient storage solutions. Whether for residential, commercial, or industrial use, high-quality water tanks play a vital role in managing and storing water effectively, contributing to efficient water use and sustainability.